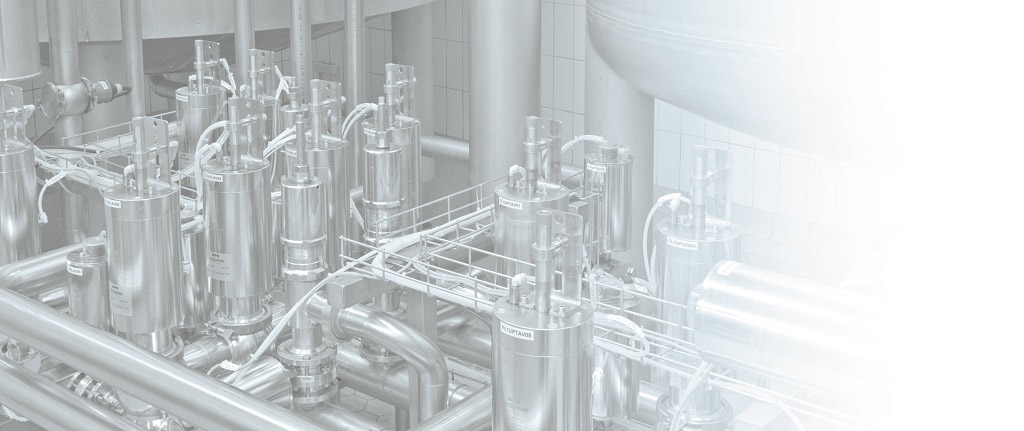
L'Industrie 4.0 c'est quoi ?
De la première révolution industrielle à l’industrie 4.0
De l’ère industrielle à l’usine connectée
L’Industrie 4.0 est aussi fréquemment nommée « usine connectée« . Il s’agit de la quatrième révolution industrielle, après celle de la mécanisation, celle de la production de masse et celle de l’automatisation.
Grâce à l’arrivée de la numérisation, l’industrie devient un système global interconnecté dans lequel les machines, les systèmes (ERP) et les produits communiquent en permanence.
Les grandes révolutions industrielles : ce qui a mené à l’Industrie 4.0
1ère révolution industrielle
Portée par la machine à vapeur (1784), la période de la révolution industrielle s’étend de la fin du 18e siècle au milieu du 19ème siècle. Née au Royaume-Uni grâce à l’extraction du charbon, cette révolution industrielle est aussi française, du fait de la commercialisation des premières machines mécanisées (machine à coudre).
2ème révolution industrielle
Liée aux énergies électrique et pétrolière, la deuxième révolution industrielle date des environs de 1890. Elle ouvre la voie à la production de masse, grâce à la transformation de matériaux tels que l’acier et l’aluminium. Le système du convoyeur (1870), inauguré dans l’industrie automobile par Henry Ford, permet la naissance du travail à la chaîne, plus rapide et moins coûteux.
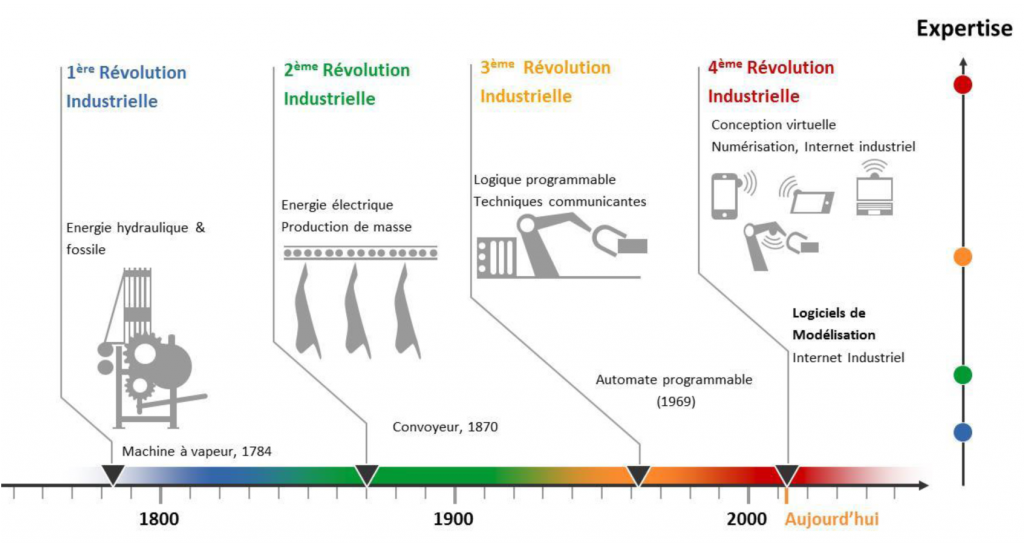
3ème révolution industrielle
Née au 20e siècle entre Etats-Unis et Japon, la troisième révolution industrielle fait appel à l’informatique (ordinateurs et mémoires programmables). Grâce à l’électronique, il devient possible de mettre en place une production automatisée (automate programmable), tandis que l’électricité nucléaire ouvre des champs de recherche menant à de nouveaux matériaux, très utiles à l’industrie. Ce sont également les prémices d’Internet.
4ème révolution industrielle
Depuis quelques années, nous vivons la 4e révolution industrielle. Egalement appelée Industrie 4.0, elle dématérialise la gestion de la production en connectant les machines et objets à Internet (Internet des Objets ou IoT). Cette mise en réseau des systèmes de production contribue à leur quasi autonomie : c’est l’Internet industriel (IIoT pour Industrial Internet of Things).
Ainsi, une entreprise 4.0 est une entreprise ayant amorcé sa digitalisation et où la convergence entre organisations physique et digitale créent de nouvelles interconnexions autant pour l’humain que pour les machines.
Les apports de l’Industrie 4.0 : l’utilisation de la donnée
L’Industrie 4.0 (ou « Industrie du futur » en France) a pour but de conserver et développer une activité industrielle forte, innovante et créatrice d’emploi. L’interconnexion permet aux usines de devenir plus compétitives grâce à un niveau de performance et de sûreté accru. Elles produisent ainsi à la fois des produits personnalisés et les services associés.
L’innovation liée aux technologies 4.0 a permis la transformation industrielle d’un modèle traditionnel vers l’usine du futur.
Sous l’essor des développements industriels ou l’accélération des lignes de production, de nouvelles solutions ont vu le jour, répondant chacune à des besoins techniques naissants. La maintenance 4.0 des équipements industriels, la robotique mais également le contrôle de la consommation énergétique sont des thématiques récurrentes auxquelles il est possible d’adresser une réponse hautement technologique, basée sur la donnée, à la fois fiable et concrète.
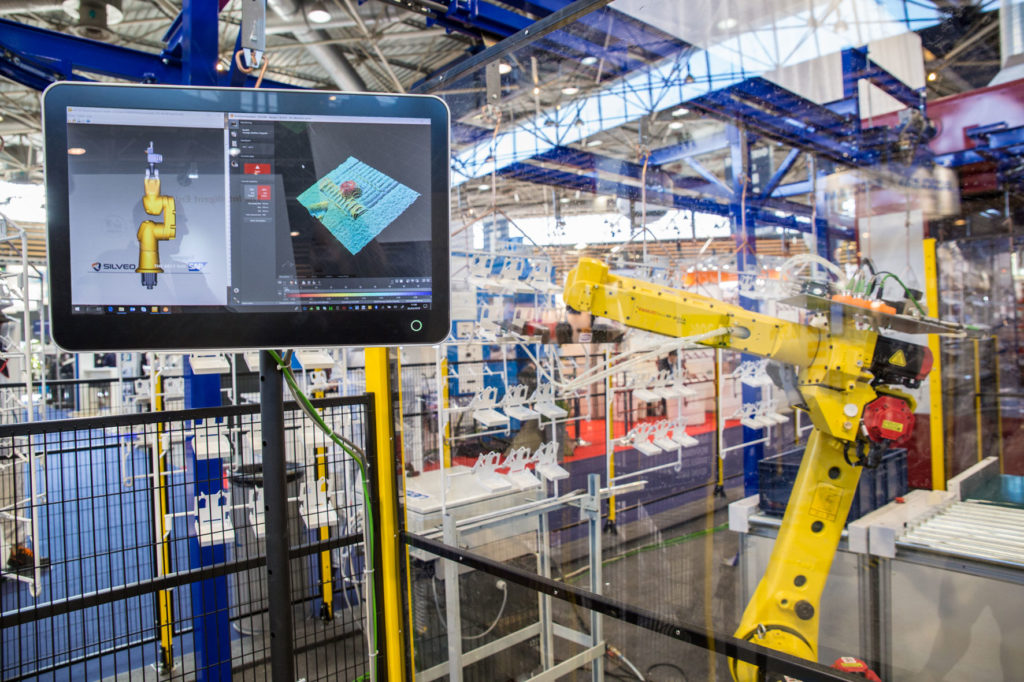
Comment faire entrer l’inDuStrie française dans l’usine 4.0 ?
Les moyens pour opérer la transition vers l’Industrie du futur 4.0
La transition vers une « factory 4.0 » permet principalement un pilotage de production plus précis et une maintenance industrielle des équipements moins coûteuse et plus anticipée. Ces solutions 4.0 se déclinent de multiples façons et peuvent être mises en place progressivement, suivant vos priorités et budgets :
- Des usines en réseau à la fois avec leurs clients et leurs fournisseurs ;
- Des modes de production flexibles, donc entièrement reconfigurables, capables de fournir des produits personnalisés et compétitifs ;
- Une optimisation des performances des lignes de production par l’analyse de la remontée des données et des informations dans le cloud ;
- La mise en place de moyens pour assurer une maintenance prédictive ;
- Un suivi économe des consommations d’énergies et des matières premières ;
- La suppression des tâches pénibles par l’apport de la robotique collaborative ;
- L’utilisation des moyens virtuels pour la simulation des procédés et l’optimisation de la maintenance des lignes ;
- L’intégration de l’internet des objets dans les produits fabriqués pour une traçabilité précise, une remontée des données pour optimiser le pilotage de la production, la logistique et l’utilisation des produits ;
- La mise en place de formations continues pour accompagner les opérateurs à l’évolution des moyens de production.
Le potentiel de la révolution industrielle 4.0
Comme l’indique ci-dessous le cabinet Roland Berger, le potentiel de l’industrie du futur et de la data industrie est encore vaste. De nombreux sujets continuent d’être développés et pourront faire l’objet d’une évolution 4.0 pour les usines actuelles.
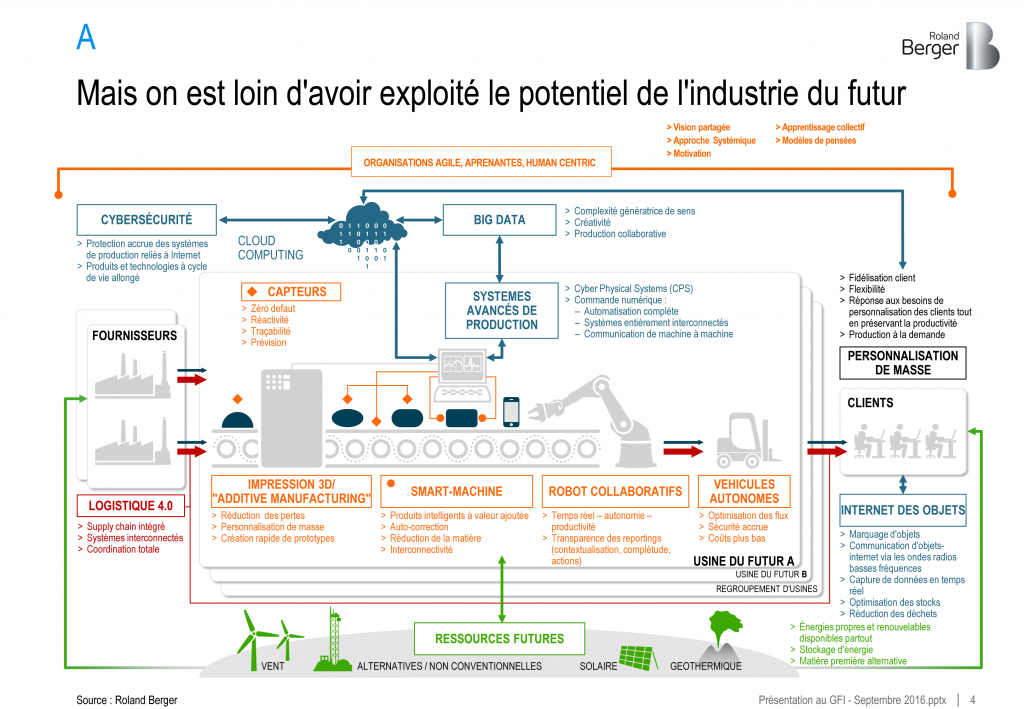
Au cœur d’une organisation agile (lean management) plaçant l’humain au centre, la transition est amorcée entre production de masse et personnalisation de masse. Le développement de machines flexibles permet d’ajuster la production aux besoins ou envies réelles du marché, avec un temps de réaction plus court. Ce dernier est souvent facilité à la fois par l’émergence des smart machines et par une relocalisation progressive de la production.
Quelles évolutions voit-on émerger dans les usines 4.0 ?
Capteurs numériques
Tout commence par le choix de capteurs numériques IO-Link. Dotés d’une intelligence interne (edge computing) et présents partout, ils sont le centre nerveux de la machine. Ils ont la capacité de discriminer les informations collectées :
- certaines sont traitées en temps-réel par le capteur, permettant une plus grande réactivité dans la production (exemple : enclencher un actionneur sur la base de telle information reçue par le capteur) ;
- des informations de diagnostic (smart sensor) sont remontées sur une interface dédiée, permettant une maintenance préventive conditionnelle : niveau d’encrassement de la cellule, temps d’utilisation, température interne du produit, pic de production, …
- en parallèle, de nombreuses autres informations de détection et mesure (lien page moneo) parviennent au centre de données, pour enrichir un historique permettant toujours plus de prédiction et de connaissance de sa production.
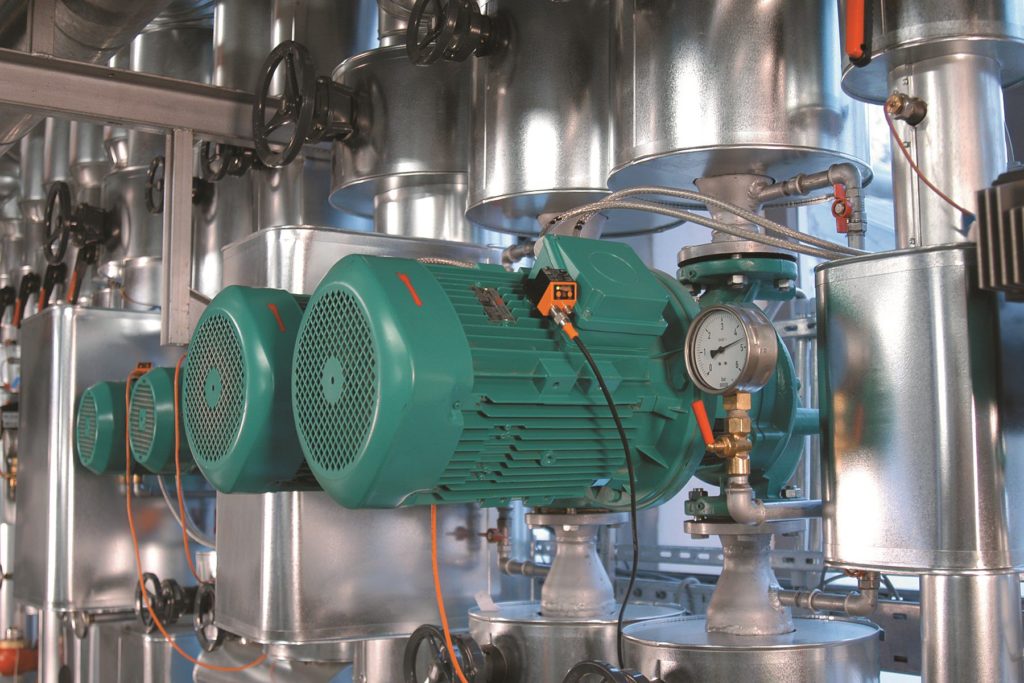
Smart machine
La smart machine est celle qui apprend (machine learning). Sur la base des informations remontées par les capteurs numériques, elle stocke des données de fonctionnement et peut ensuite se corriger elle-même, voire s’assurer de la qualité des pièces produites. Cette interconnectivité (communication amont et aval) pourrait aussi permettre de placer la confection d’un produit à la carte au sein d’une production de série : une vraie révolution pour la logistique 4.0 !
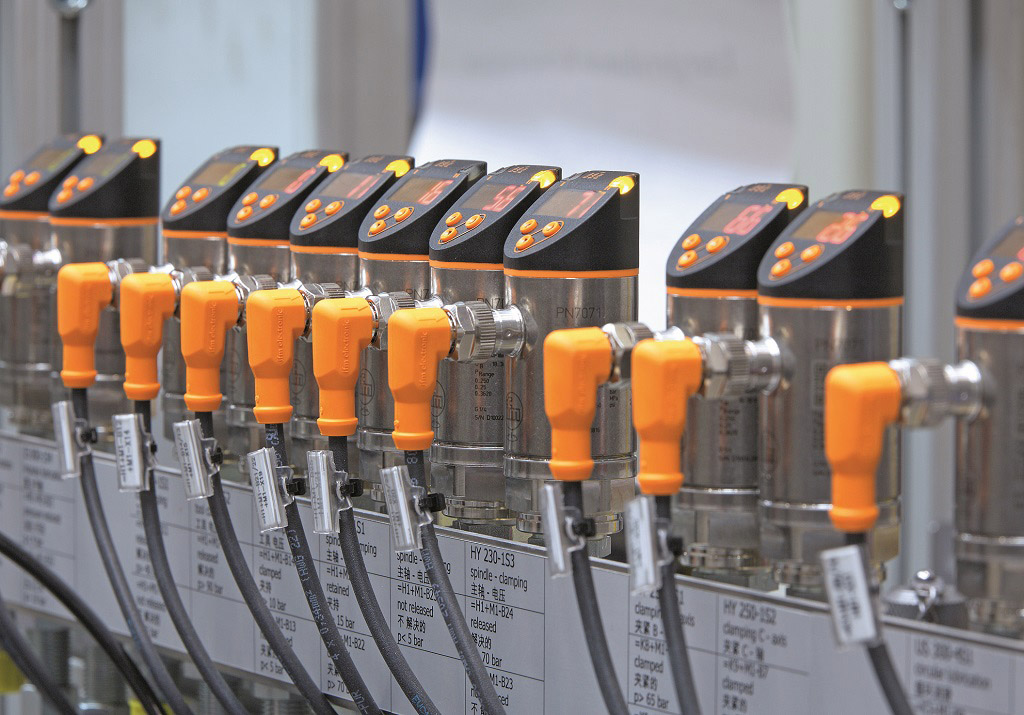
Internet des objets
Valeur ajoutée indéniable des entreprises de service, la communication d’objets via internet ouvre le champ de leurs prestations et de la satisfaction client. Connectés à l’aide de réseaux LoRa (bas débit), les objets peuvent informer le fabricant ou le détenteur de leur état (panne imminente) ou du type d’utilisation qui en est fait (fréquence, cadence, …).
Les capteurs IIoT permettent cette remontée de données précises auprès des entreprises IoT (industriels, fabricants). La plateforme moneo d’ifm peut ensuite leur donner de la valeur via un monitoring ou une historisation pour analyse future : c’est l’immense gain offert par la jonction entre IoT et intelligence artificielle.
Big Data
Les flots d’informations nécessaires à l’analyse doivent être utiles à la production sans pour autant ralentir les automates. Ils doivent donc transiter par un canal différent : c’est ce que permet la technologie IO-Link, en répartissant les flux de données. Cette technique est aussi appelée edge gateway.
Robots collaboratifs
Alors qu’auparavant, les robots œuvraient seuls et à une cadence élevée, ils doivent aujourd’hui pouvoir travailler en collaboration avec les humains, notamment pour les soulager des tâches pénibles et limiter les TMS. Certaines catégories de robots sont également capables d’alterner une cadence élevée en l’absence d’humains et une cadence plus collaborative lorsqu’il y a des opérateurs dans leur zone de travail.
L’industrie 4.0 c’est quoi ? Tout savoir sur l’Industrie 4.0
Pour approfondir le sujet, nous vous conseillons les documents suivants :
Publications
– Gimélec : les leviers de la transformation
– Gimélec : l’usine connectée
Vidéos
– FIM : Industrie du Futur